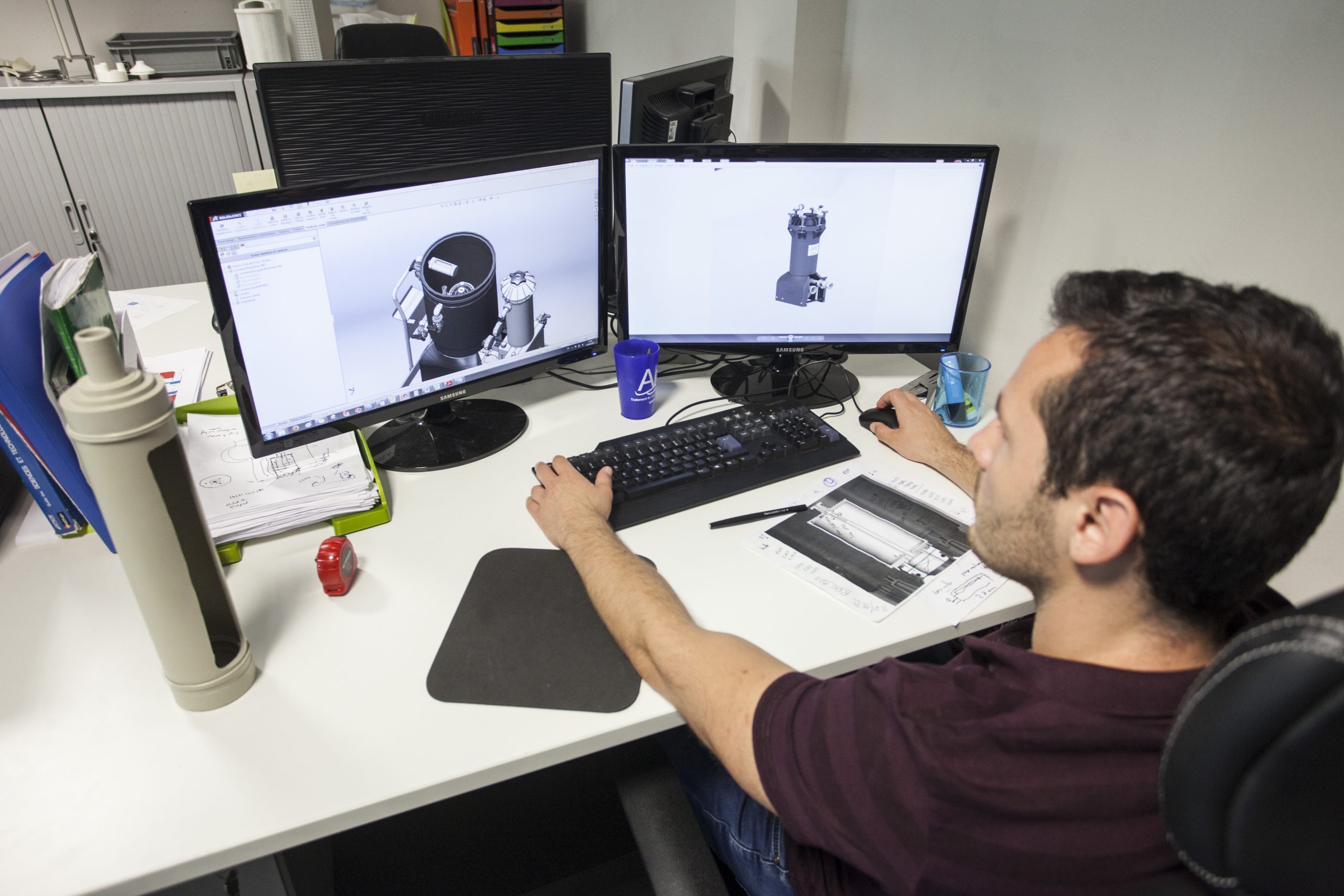
Calibrate your Venturi mixing system.
In order to optimize your bath agitation, many parameters must be taken into account.
The number of nozzles
The number of mixing nozzles depends on the total length of the tank and the recommended spacing between the nozzles according to the table at the bottom of the page.
Nozzle size
The size of the nozzles depends on the size of the tank and the space available. Often, tanks under 300 liters are equipped with ¼” agitation nozzles. Larger tanks are primarily equipped with ⅜” agitation nozzles and deeper tanks may benefit from the use of ¾” agitation nozzles.
Piping Design
The design of the piping system must allow for homogeneous bath stirring, avoiding excessive turbulence on the parts being electroplated. Pickling or cleaning applications support higher turbulence.
Pump power
The choice of the pump is calculated according to the number and size of the selected stirring nozzles, the depth of the tank and the complexity of the tank.
Nozzle support
In order to facilitate the installation of the nozzles, you can opt for a specific support to screw the nozzle directly on the pipe. We have developed brackets in PVC, PP and PVDF to fit the pipe and increase the rigidity of the connection. There is no need to thread the pipe, a simple drilling allows to insert the nozzle support. The support is then welded by bead or by socket.
SIEBEC fluid simulation for a perfect result.
As you can see, bath agitation with Venturi nozzles can be complex due to the many parameters that come into play in the development of the system. This is why we accompany our designs with 3D fluid simulations to optimize the circuit.
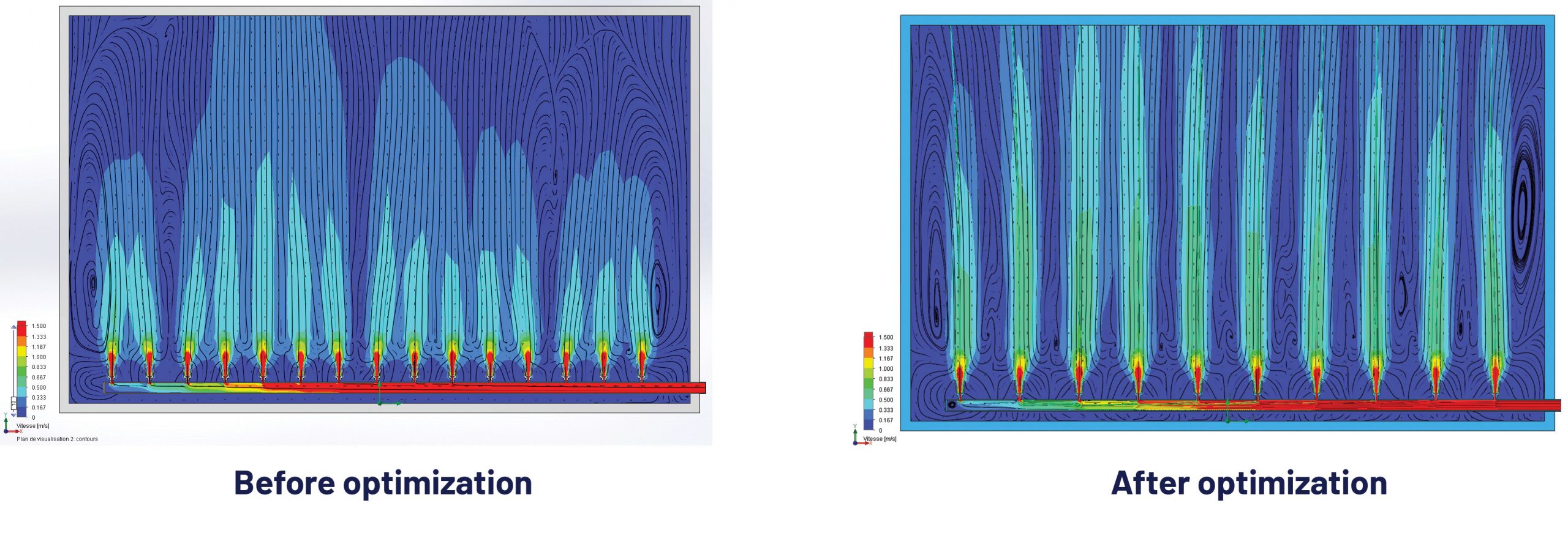
Example: Simulation of savings
Comparison of a conventional air agitation system and the SIEBEC Venturi system.
- Volume of the tank: 5 m³.
- Bath temperature: 60°C
- Air temperature: 20°C
- Power consumption (Venturi agitation) : 12 kW
- Power consumption (air agitation) : 15 kW
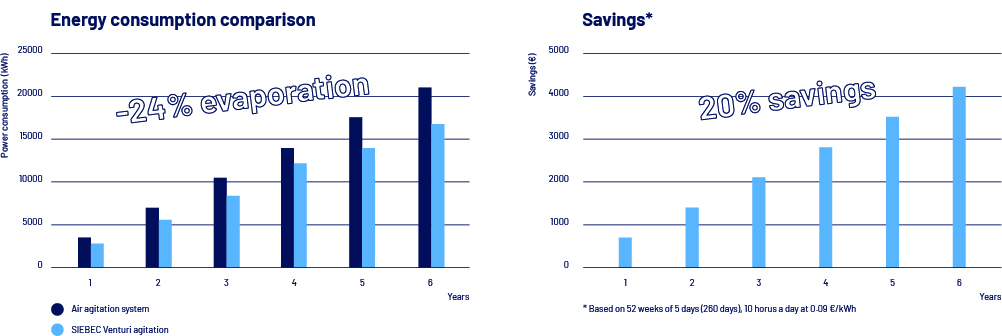